Our policy of continuous improvement is achieved through:
Involving the whole workforce, conducting regular system reviews
Establishing a suitable, safe working environment for our employees
Developing quality driven processes that are monitored at each stage
Continuous development of Operator skills, and employing the latest 3D design modelling systems
Developing objectives for all areas of the business.
This quality system has the full commitment of Gascoyne and Beever’s workforce and the Management team. The Quality System includes detailed Non- Conformance monitoring and is understood by all employees and is implemented through working with the Companies Quality Management system. The Quality system is based on Our Alcumus ISOQAR Approved Certificate of registration Ul<CA Factory Production Control system and is designed to be in compliance with BS 9001 standards.
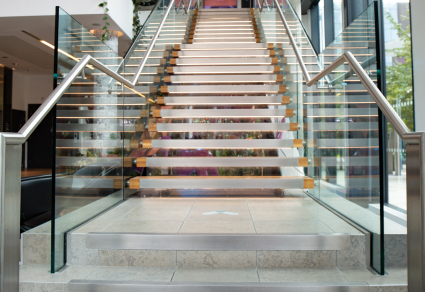
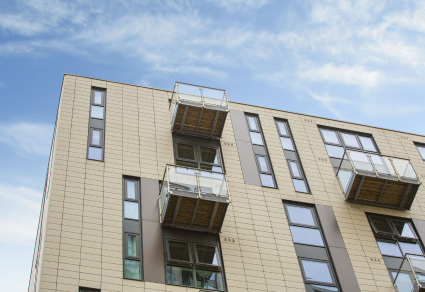
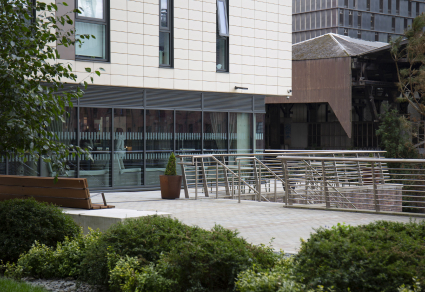
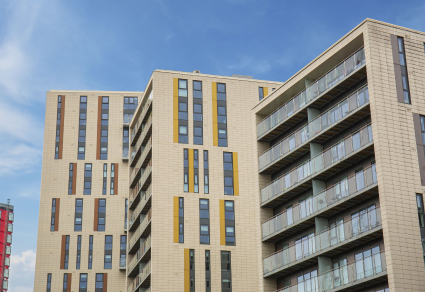